Loading
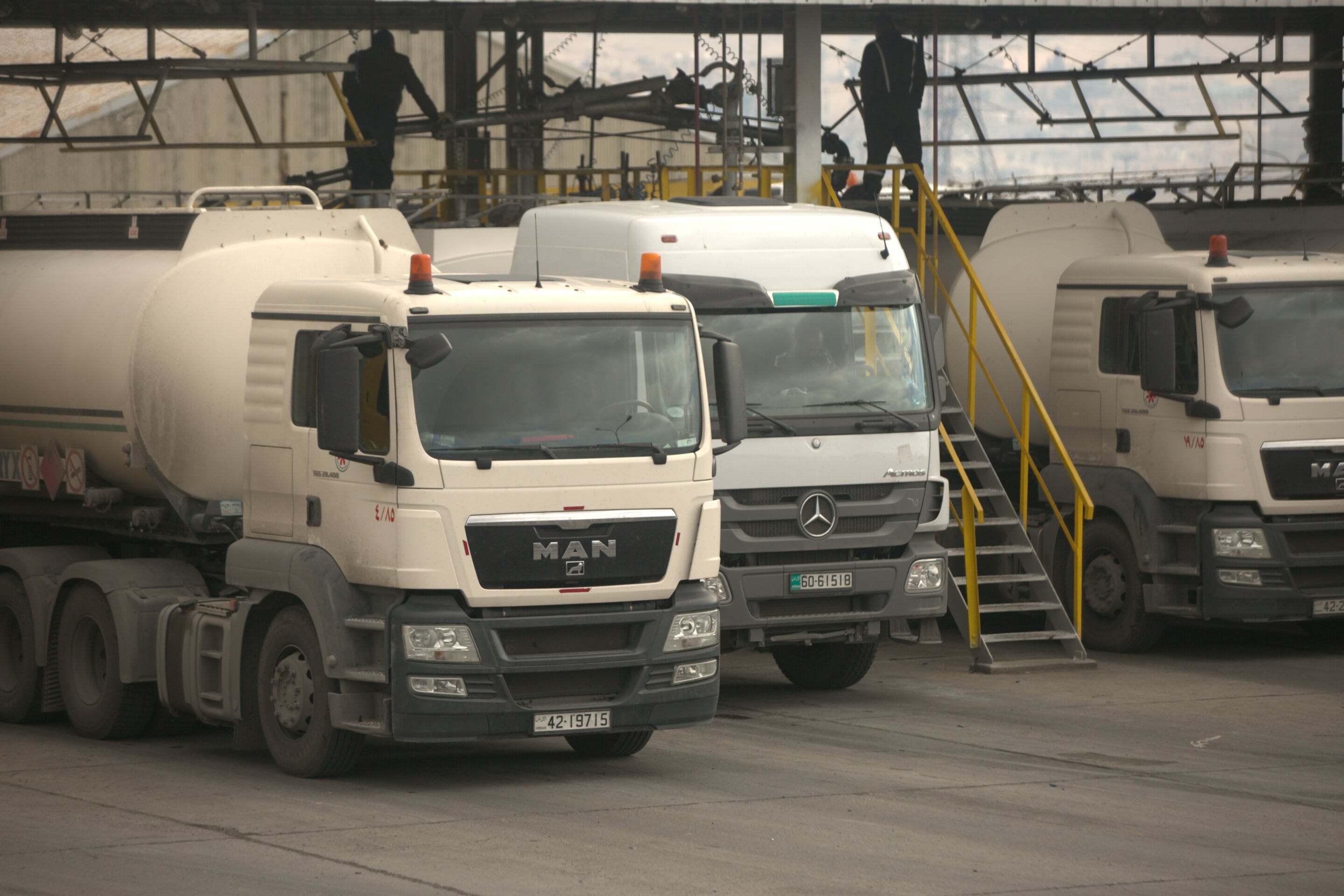
The Department of Derivatives Movement and Loading at the Jordan Petroleum Refinery Co. is concerned with the loading of petroleum derivatives of different kinds and specifications (LPG, gasoline 90/95, kerosene, normal/special diesel, normal/special Avtur, fuel oil, white spirit, and asphalt grades) in tankers affiliated with the three marketing companies' fleet, or in private tankers specialized in fuels services.
Asphalt is also loaded in barrels dedicated for this purpose.
In confirmation of the provision of distinguished service to the public and preservation of the highest levels of quality in work, performance and sale, tankers and tested and inspected before loading to ensure its safety and readiness for loading as well as the availability of public safety in it. Tanker is also tested after loading to ensure matching between the kind of loaded material with the loading permission, as well as conformity between the cargo and axial load of the tanker, and then it is sealed with special sealing to prevent any tampering during transportation to customers.
For testing purposes at the Department of Laboratories and Quality Control, samples are also taken from the material loaded in the tanker whether before unloading (in case of unloading of imported petroleum materials) or after loading (in case of loading of petroleum derivatives) to ensure its compatibility with the specifications approved by the Company before conducting any act regarding the tanker. If any case of incompatibility is found, this will be directly dealt with inside the Department according to special procedures and instructions on case by case basis, and all of this is documented in the records of the Department in order to review and identify reasons to prevent reoccurrence of such case.
The Department also receives crude oil imported to the refinery at the station of crude oil loading located at the refinery site, where (2072520) ton were received in 2020 in order to be refined into petroleum products, as it also receives the imported petroleum products to be stored in the refinery tanks, (53782 tons) of Gasoline-90, (36045tons) of Gsoline-95, (36943 tons) of Avtur, and ( 56903 tons) of MTBE were received in 2020.
The Department is committed to the safety regulations adopted by the Company as well as the international regulations of public safety during the operations of loading and unloading, and violators are subject to the most degrees of punishment according to the internal regulation of the Company to prevent any future violations.
Annual training courses are held in cooperation between the human resources and the training center of the Company in order to train the employees of the Department to the procedures of safety and first aid, as well as the actions to be followed in emergencies and how to deal with the petroleum derivatives, within a training program prepared specially for this purpose and implemented by individuals specialized in this field, in addition to the continuous field training for employees by the person in charge at the Department. Noting that the Emergency and Evacuation Plan was prepared according to the international references
The Department also hands over written instructions of public safety to the drivers from outside the staff of the Company and takes their signatures on these instructions before allowing them to
access the Department of loading. In case any violations committed by drivers, dissuasive penalties are taken against them (according to the penalties regulations of drivers) and this would prevent any future violations.
ISO 9001:2008 was obtained in 2008 till 2017.
ISO 9001:2015 was obtained in 2018.
Paying attention to customers satisfaction, meeting the needs of customers, and decreasing the time spent in the works of loading and unloading are the most important priorities of the Department and they are given the highest degrees of attention and follow up by the administrators because it have a significant impact on the service provided to citizens and the interest of the homeland; therefore, the Department through the Information Systems Department of the Company had updated the system of loading and unloading with the latest update "J.D. Edwards" for all activities of the Department .In addition updating the system of dealing and monitoring the movement of tanks through an electronic tablet from the entry gate to the exit gate.
Any complaints or comments provided by a customer are received by the Complaints Boxes distributed in the Department, or through the Public Service Office at the Company, and then each complaint is passed via official channels to the Department of Derivatives Movement and Loading (in case it was related to this Department) in order to be followed up and settled officially after being documented, and then the complaint or comment is analyzed at the meetings of the Management in order to identify its reasons and prevent its future occurrence. A periodical questionnaire is carried out at the site of the Department according to a special procedure prepared solely for this purpose, and then the information collected are discharged in special tables in order to be analyzed for the measurement of customers' satisfaction.